国内外涂装前处理技术标准差异
涂装 前对被涂物件表面进行的一切准备工作,通称为被涂物件的表面处理(简称前处理)。由于科学技术的不断进步,涂装在现代生活中的应用愈来愈广。所以涂装前处理的范围应包括各个方面。由于目前汇编的涂装国内外技术标准,基本上未涉及有色金属、木材、水泥、塑料、纤维、橡胶、玻璃等,所以本文仅对黑色金属前处理加以论述。
一、 表面处理的目的:
1、清除被涂物件表面上存在的各种污垢和影响涂装的各种附着物。如油、脂、锈皮、轧钢所产生的氧化皮、焊渣、灰尘、归漆的涂膜等。因为有这些物质附着在被涂物表面上就必然会影响涂装的效果。不但会影响涂膜的外观,而且直接影响着涂膜与被涂物的附着力,从而达不到预期涂装保护基体和装饰基体的作用。
2、修整被涂物表面存在的缺陷,如焊接飞溅物(焊缝之外的焊粒)孔隙、凹坑、机械加工所产生的锐边、触点(由于保存不好而造成明显的腐蚀深坑与麻点)以及夹缝、裂缝、缝隙等等。这些被涂物表面的缺陷,不但会影响涂装涂膜的质量,甚至会严重的影响整个部件或设备的寿命,是必须在涂装前彻底清除的。在清除的过程中,还应达到被涂物在涂装时所需求的表面光洁度(应特别指出表面光洁度不是越光洁越好,太光洁也会影响涂膜与基体的附着力,使涂膜有良好的涂装基础。一般认为被涂物的表面光洁度应在 4—6 级范围内,较为合适。
3、对被涂物表面在涂装前进行各种方式的化学处理(如磷化、钝化、植酸盐转化等)以提高涂膜对基体的附着力和防腐蚀能力。由于现代社会对涂装的要求越来越高(特别是小轿车表面涂装),所以对不同材质的被涂物的涂装前化学处理越来越被人们所重视。
在美国 1982 年钢结构涂装协会颁布的表面准备技术规范(SSPC-SPCOM)中特别指出:“涂膜的寿命很大程度地取决于表面准备的程度”。因为准备的不好,就会导致涂膜过早的失效而达不到预期的目的。在文章的叙述中,使我们感到美国对于表面准备工作特别重视,他们认为这是涂装工作做好做坏的关键,是直接影响涂膜过早失效的根本原因。SSPC-SPCOM 中特别指出,涂膜大多数过早失效都是与不适当的表面准备或涂膜无附着力有关。正因为如此,他们不厌其烦地颁布了一系列技术标准。
3.1 SSPC-SPl 溶剂清洗:利用溶剂、汽、碱、乳化作用或蒸汽清洗除去油、脂、灰尘、污物、盐和污染物。
3.2 SSPC—SP2 手工工具清理:用手锉、刮、砂和刷除去疏松锈、疏松轧皮、疏松涂膜到规定程度。
3.3 SSPC—SP3 动力工具清洗:用动力工具锉去氧化皮,砂、刷和磨去疏松锈、疏松轧皮、疏松涂膜到规定程度。
3.4 SSPC—SP5 金属喷白色清理:藉助轮子或喷咀,用砂粒、丸或喷射清理去明显的锈和外来物(强腐蚀气氛要保证用高成本清理。)
3.5 SSPC—SP6 工业喷射清理:至少喷砂清理到表面积 2/3 无各种明显的残物。(用于很严酷的暴露条件)
3.6 SSPC-SP7 喷射除去清理:除去牢固附着的残余轧皮外,喷射清理去一切锈和涂层,暴露许多均匀分布的底金属斑。
3.7 SSPC—SP8 酸洗:用一次酸洗,二次酸洗或电解酸洗,完全除去锈和轧皮。
3.8 SSPC-SP1O 金属喷白色清理:喷射清理到白色金属的清洁度,至少要到 95%表面积都无各种明显的残渣(用于高湿度、化学氛围、海洋或其他腐蚀性环境。)
二、在表面处理的要求上,美国标准与我国标准的差异
美国标准与我国标准相比,要严格一些:
l、美国标准中表面处理应除去典型的污染物:潮气、油、脂、氧化物、硫酸盐、锈、腐蚀产物和灰尘等。
2、表面前处理要使被涂覆的表面能获得与涂膜良好的附着力和容易润湿的表面。
3、美国标准认为大多数涂膜的过早失效是与不适当的表面准备或涂膜无附着力有关。这就要求我们对不同的材质、不同要求的涂膜质量,选用适用于这些要求的前处理方法。
4、SSPC-SPCOM 特别指出,在环境条件很严酷时,表面缺陷也会造成涂膜的过早失效(特别是边缘和突出部位以及附着力差的污染物等),该标准认为:必须花大力气,用较多的时间去对表面缺陷进行修理工作。这些缺陷包括:残留焊渣、疏松的焊接飞溅物、孔隙、锐边、触点、夹层裂缝、缝隙以及腐蚀防护的不良设计区(如点焊连接、背对背的角等等),并对这些缺陷的处理方法作了详尽的描述。
笔者认为这一点很重要,必须引起我们设计和生产管理部门的高度重视。事实上,尽管大家都知道前处理对于涂膜的附着力、表面质量的好坏具有极其重要的作用,然而在实际工作中,我国在表面处理的投资上、工作质量的要求上与国外相比差距还是很大的。1994 年笔者曾到某一大型轿车厂参观,该厂设计、制造的大型轿车,曾多次获得过各种奖励,然而在前处理和焊接工件上,竟能看到部件上的残液的痕迹、锈迹,磷化质量不好(较差)及焊缝质量不好的部件也能顺利地流入下道工序。
为了保证涂装质量,在大型生产流水线上,绝不能忽视前处理各工序间的检查,应该做到不合格的部件坚决不能流向下道工序。
5、对于涂装前钢材表面锈蚀等级和除锈等级方面的差别
5.1 在表面锈蚀方面
我国 GB8923-88 中规定的钢材表面锈蚀的 A、B、C、D 四个级别与美国 SSPC-SPCOM 新结构中所叙述的四个等级,S1S055900-1967 瑞典标准中所叙述的原始锈蚀的内容大体相仿。
A 级:全面地覆盖着氧化皮而几乎没有铁锈的钢材表面。
B 级:已发生锈蚀,并且部分氧化皮已经剥落的钢材表面。
C 级:氧化皮已因锈蚀而剥落,或者可以刮除,并且有少量点蚀的钢材表面。
D 级:氧化皮已因锈蚀而全面剥离,并且已普遍发生点蚀的钢材表面。但美国 SSPC-SPCOM 当中对维修钢表面的锈蚀情况进行了分类,这是我国标准当中没有涉及到的。该标准对涂装过的钢材表面也划分了四个等级,代表维修再涂装时钢材表面的初始化状态。即 E、F、G、H 四个级别。
E 级:涂膜几乎完整无损,可出现底漆,锈蚀覆盖面小于整个表面的千分之一 (SSPC-VIS-Z 锈蚀等级 8-10)。
F 级:面漆有些风化,可出现底漆,轻微花斑或起泡,擦去花斑后出现锈蚀、起泡、疏松轧皮或疏松漆膜的面积小于总面积的百分之一。(SSPC-VIS—2 锈蚀等级 6-8 级)。
G 级:涂膜完全风化起泡或发花斑、锈蚀、起泡、硬皮或疏松漆膜等覆盖面积达到整个表面的百分之十,明显
蚀点很少。(SSPC-VIS2 锈蚀等级 4-6)。
H 级:大部分表面有锈蚀(蚀点、锈针)和无附着性的涂膜覆盖,缺点明显(SSPC-VIS2 锈蚀等级 0-4)。
E、F、G、H 四个等级的划分是按锈蚀的百分率来计算,每个等级间相差 10 倍(即 0.1%、1%、10%、100%)其图谱在 SSPC-VIS2 中有所表示。SSPC-VISl 表示新结构的标准图谱。
5.2 在除锈方法方面
我国在 GB8923—88 标准中叙述的除锈方法。
5.2.1 喷射或抛射除锈
5.2.2 手工和动力工具除锈
5.2.3 火焰除锈:火焰除锈前,厚的锈层应铲除,火焰除锈应包括在火焰加热作业后以动力钢丝刷清除加热后附着在钢材表面的产物。
(SSPC-SP4 为美国新钢的火焰清理标准,此标准已于 1982 年中止)
火焰除锈中所述的附着物包括焊渣,焊接飞溅物、可溶性盐等,氧化皮、铁锈或涂膜层能以金属腻子刮刀从钢材表面剥离下来的附着物,被看作为附着不牢。这一标准由中船总公司、铁道部提出。笔者认为它有—定的局限性。火焰除锈法目前在国内外大多数厂矿都很少使用。此法虽然简单,但对部件会产生不利因素,特别是对一些薄钢板,如热变形、局部过热、产生热应力等等,会严重影响产品的质量。所以,火焰除锈只能用于厚钢板及大型铸件,这一点应在标准中特别提及。
有关喷射、抛丸及手工、动力除锈,我国及瑞典标准讲的都比较简单,然而在 SSPC-SPCOM 美国标准中,对于喷射清理作了极其详尽的论述。如对磨料的选择、钢丸钢粒的类型、使用范围,以及非金属磨料的物性、类型及其使用范围和产生灰尘的限制,都作了详尽的规定。由此可见美国对钢铁表面的锈蚀去除是经常采用此法。应特别指出喷射或抛射,主要应用于黑色金属或厚板材,但也可应用于轻金属和薄壁金属。但薄壁金属在喷射清理中应特别小心,因为过度喷丸强化会产生翘曲或损伤。
三、我国对“四合一、三合一、二合一”的前处理办法是加以认可的,该标准规定了“以磷酸和磷酸盐为主要成分,添加其他助剂所组成的表面处理液,可以对钢铁表面完成除油、除锈、磷化、钝化功能的称为四合一处理液。可完成除油、除锈、磷化(或钝化)的处理液为三合一。可完成除锈、磷化的称为二合一处理液。”
该标准由航空航天部提出,并以国标的形式加以推广。“四合—、三合一、二合一”应该说是我国在前处理工作中的一种创造。在国外众多工艺和技术标准中很少见到,它在简化工序、减少劳动强度等方面确有一定的优越性,在七十、八十年代曾风行一时,近年来应用此种方法的单位越来越少,为什么呢?笔者认为这种多功能处理方法的致命弱点恰恰就在多功能上,抛开此法操作管理复杂、难以很好控制的缺点外,在大批量的生产中,虽然它面面都加以涉及,然而,哪一种功能都很难满足越来越高的涂膜对基本表面前处理的要求。正因为如此,目前新建的大型涂装线,如汽车、家电等没有一家采用此种方法。
这种多功能处理液,不但需要进一步提高其技术水平及功能效果,而且在应用上也只局限在小批量的零部件或实验用的样片上。当然从节能、节约资源、提高效率上,不可否认有一定的优越性,但由于它很难满足高水平涂膜对基体前处理的要求而使其发展受到一定的限制,正如有些包治百病的药物一样,什么病都能治,但什么病也治不彻底。任何事物都有其自身的局限性,包打天下的事是绝对不可能的。
四、溶液清洗方面
SSPC-SPCOM 中明确指出溶剂清洗主要用于去除油、脂、尘土、污物、拉拔化合物和其他类似的有机化合物,也可作退漆剂或碱性退漆剂除去旧有的涂膜、无机化合物,但氧化物、硫酸盐、焊渣、锈、轧皮是不能用有机溶剂去除的。我国目前用于涂油的方法大体上有以下几种:
1、有机溶剂除油:利用有机溶剂对油脂的溶解作用而将油污去除。对有机溶剂的一般要求如下:
1.1 对油脂要有较强的溶解能力。
1.2 毒性要小,且不易燃烧和爆炸。
1.3 价格低廉、易于回收重新利用。
1.4 对环境和生态不会造成危害等。
目前最常用的溶剂有汽油、煤油、松节油、酒精、二甲苯、三氯乙烷、三氯乙烯和四氯化碳等,我国多种资料都对三氯乙烯气相除油作了较详细的报导。认为它是一种比较优异的有机溶剂清洗法。其原因是三氯乙烯沸点较低(87℃),易于气化和冷凝,且蒸汽密度较大,不易扩散,不易燃烧,溶解油污能力较强等一系列优点而加以采用。
然而在 SSPC-SPCOM 中明确指出溶剂清洗可采用氯化烃,但由于毒性,一般还是不采用氯化烃为好,利用该法只限对工件有特殊要求和操作者训练有素的情况下方可采用。并对采用时氯化烃在空气中的浓度作了较严格的限制。
四氯化碳一皮肤 5ppm、环氧氯丙烷一皮肤 2ppm,二氯乙烯为 10ppm,三氯乙稀为 50ppm,二氯甲烷为 100ppm。
这些限制的目的,就是要保证操作人员的健康不致受到损害。在这方面苏联对车间有害物质的最高允许浓度要比美国、日本严的多:
在要求溶剂作用较大的情况下,也可采用芳香族或煤焦油溶剂,但对于苯,因为毒性较大,特别提出不宜使用,若考虑到闪点[苯的闪点较低-11℃(闭口)],具有爆炸危险时,就更不宜采用苯,建议用混合二甲苯、二甲苯或高闪点的汽油加以代替。这与我国目前应用的情况有较大的区别,在我国不少工厂用苯作溶剂的情况还是很普遍的。
2、碱液清洗除油:目前我国常用的碱洗配方多以 Na0H 为主,或 NaOH 再加配一些其他碱性化合物如 Na2C03、Na3P04、Na2 Si03 等,其工作温度较高。但 SSPC-SPCOM 标准指出美国最常用的碱洗清洗剂为 Na3P04。(有时也采用一些其他碱金属的磷酸盐并加入一些润湿剂和去污剂的混合物,多为专利产品。)
3、乳化除油:利用乳化剂将有机溶剂分散到水中形成乳化液,它可使油脂溶解,将其去除。常用的配方为:
煤油 67%、月桂酸 5.4%、松节油 22.5%、三乙醇胺 3.6%、丁基溶纤剂 1.5%。机械部颁布的 JB4323-86 水基金属清洗剂就是这类产品,它是由表面活性剂和多种添加剂组成的清理金属材料及其零部件表面上油污的水基金属清洗剂。此法可减少着火和中毒的危险。我国不少科研单位,在这方面都取得了可喜的成果。
为了提高乳化除油的效率,有时还采用超声波振荡去油。与我国不同的除油方法是蒸汽清洗法,即用含碱液或表面活性剂、去污剂的蒸汽及加压热水去除油污的办法。在美国除油标准中还特别指出了清洗,因为碱液或其他方法除油时,工作一定时间后,一部分油污会漂浮在槽液上面,致使被除油工件再次粘附上油污,所以处理后的工件一定要用清净水将其冲洗干净,否则会影响涂装效果。
五、关于溶剂在工作室中的最高允许浓度
SSPC-SPCOM 所列举的有关溶剂在工作室的最高浓度,是美国政府于 1984-1985 年所确定的文件中明确规定“这些数据每年都要进行修订,在应用时,应按照最新的标准予以执行,否则是不合法的”,这足以说明人们对化学溶剂和有关物质的认识是在不断深化和加深理解之中,其目的就是为了能够选取最经济、最有效、最安全可靠的工作方法,这合乎人们对事物认识的客观规律。
废气排放的安全规范在不同国家有着不同的标准,就苏联、美国、日本与我国相比:苏联标准最严;美、日较松,我国介于二者之间。从花费的经费等方面来对比,苏联最大,美、日较少,我国介于二者之间。究竟哪—个标准正确?哪一个标准最合理、最切合实际?是值得我们深思的。哪一个标准所规定的数据既能满足工作环境的要求,又能保证安全生产和最小投资,就是一个切合实际的标准。这就给设计工作提出了一个经济化设计的要求,西方国家在整体设计中非常重视整体的寿命时限,我们在不少设计中富裕量很大,而且部件与构件、零件之间的使用寿命都不同步,这是一个很大的缺点,应该加以改正。
六、酸洗
美国 SSPC-SP8 中所述的酸洗概念比我国机械部 JB/T6978-93 行业标准的含义要广一些,sP-8 中指出:酸洗是一种利用化学反应、电解或者兼用所进行的钢构表面准备方法,在没有放大的情况下对表面进行观察时应无轧皮和锈的处理方法。我国目前所使用的方法大多都是化学方法,很少涉及到用电化学方法进行酸洗。
在具体操作方法和程序上,美国 SP—8 酸洗标准比 JB/T-6978-93 规定的更加详细、更加具体,笔者认为我国规范中没有提及或讲述不够详细的地方,恰恰可能就是我们工作中最需要注意的。
1、SP-8 中明确规定:“为保障酸洗的质量和能够使酸洗工作正常运作,在酸洗前要用溶剂清洗的办法除去厚的油、脂、灰尘等其他外来物质,不允许在表面上留下有害物质。(少量的外来物体(质)是允许进行酸洗的)。
2、要利用手工工具、动力工具或工业喷射等方法除去物件表面上的锈、锈皮和涂料。不过度延长酸洗时间。也就是说不能利用酸洗槽对其进行清除,否则就会延长酸洗时间,加重酸洗槽的工作和管理负担,并会产生氢脆,过腐蚀等一系列难以克服的弊病。SP-8 指出“只有不过度延长酸洗时间,就可以除去锈沉积的工件,方可在酸洗槽中除去”。
3、在含有缓蚀剂的酸液中除去轧皮及锈之后,应在槽子上空短暂停留,滴去物件,构件上酸液最大限度地减少酸液的带出。其目的是为了尽可能的减少酸液及杂质进入清洗水中,因为酸洗后的物件必须在清洁水中充分漂洗,而且对这种水质的要求也是很高的。SP-8 规定漂洗水必须是清洁水或蒸汽冷凝后的蒸馏水,倘若有酸液带入就必需不断地加入新鲜水,这样不但会加大污水的处理量、新水的供应量,还将加大运行费用和操作者的劳动强度,SP-8规定不得带入清洗槽的物质所造成的总酸量或溶解盐量,不超过 2g/l,JB-T6978-93 也规定清洗槽中盐和酸的积累总量≯2%m/m。
4、SP-8 中还明确规定不能把未干燥的酸洗物互相堆放起来,加以接触。并应对酸洗后的物件尽快涂装,以免再次发生锈蚀。
5、SP-8 中对于安全也作了非常严格的规定,特别指出为了保证酸洗工作安全,不但要遵守联邦、州、地方法规外,还应遵从 sP-8 中要求及组成部分的安全要求。
七、磷化
在 IS09717—1990(E)金属的磷酸盐转化膜一确定要求的方法及 GBll376-89 金属磷酸盐转化膜中都明确规定:对于特殊用途的钢铁工件应在磷化前进行热处理,以消除应力和磷化后进行热处理以消除氢脆。机械加工时产生的表面应力,在 200℃或 200℃以上的温度下进行热处理可以消除。磷化后消除氢脆,对于深度冷加工钢件或抗拉强度大约为 1000N/mm2,或更高的钢制工件应在磷化、水漂洗、干燥和附加精饰后立即进行热处理。其热处理条件为 1000-1400N/mm2 时,T=130-200℃,ι≮lh;热处理条件为 1400-1800N/mm2 时, T=150-200℃,ι≮4h;热处理条件为大于 1800N/mm2 时,T=170-200℃,ι≮6h。但要注意在较高强度下,消除氢脆会引起磷化膜脱水,从而降低其耐蚀性。所以,锌系磷化膜热处理温度不能高于 150℃;锰系磷化膜不能高于 170℃。我国标准中仅提出应采用低温热处理,但无具体数据。
在我们的日常工作中,各企业的磷化作业,进行热处理清除氢脆和因机加工所产生内应力的办法并不多见,应引起我们的重视。
国际标准中还特别对表面淬火钢制件的磷化热处理进行了规定:经渗碳、火焰淬火和感应淬火并随后进行磨削加工的钢制件,应在较低温度下进行热处理(T130-150℃下,ι≮6h),GBll376-89 标准中还特别对一般合金、渗碳钢件推荐用下述方法消除氢脆:锌系磷化膜 T=98-107℃,ι=8h;锰系磷化膜 T=90-107℃,ι=8h 或室温下 120h。
其次国外标准不少地方都采用了与磷化相配套的钝化工艺,这一点在我国实际工作中,也不多见。是否需要也是我们今后工作中应摸索的一个问题。(常用钝化剂有重铬酸钾、铬酸、亚硝酸钠等,但在今天环保要求愈来愈高的情况下,过去所用的钝化剂,已被有关法规所限制。若要增加钝化工艺,寻找新的钝化剂,已被提到议事日程上来了。)
j9九游会
公司/地址
j9九游会(唐山)科技有限公司
河北唐山芦台经济开发区散热器产业园区
电话/传真
电话:18622675555/18931468400
传真:022-69351888
邮箱/网址
邮箱:contact@henso.net
网址:www.henso.net
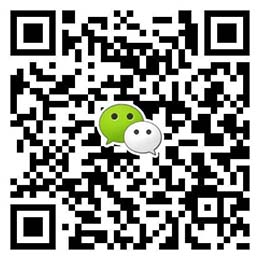